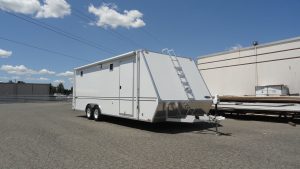
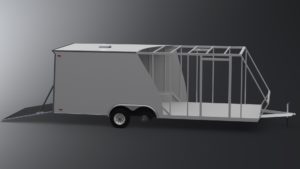
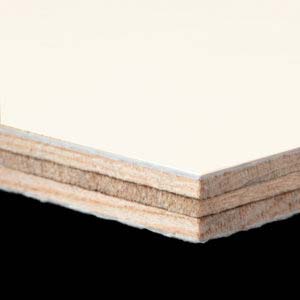
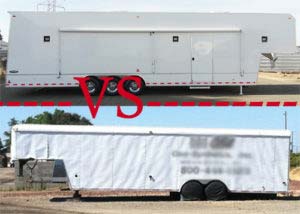
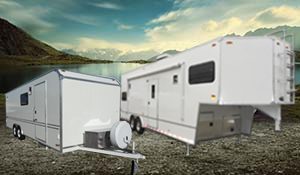
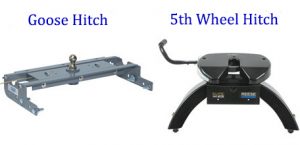
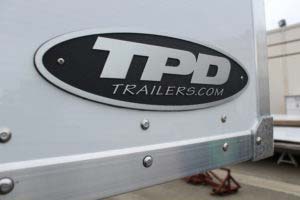
Decide on the trailer and options.
You pay the down payment, and we assign a production slot for the trailer.
Next, we will create a CAD (Computer Assisted Drafting) drawing of your trailer, with the desired options in place.
We will submit the drawing to you for your approval and signature.
At this point you should make any modifications (locations of D-Rings, Spare Tire Mount, etc.). If necessary, we will make the modifications, re-draw the trailer, and re-submit it for your approval.
When you approve the drawing, with no modifications, the trailer will be built when its production slot comes up. A Design Fee will be charged for modifications made after a drawing is approved.
After your TPD Trailer is built and goes through our thorough inspection process it is ready for delivery.